![]() |
What is an aluminium sheet?
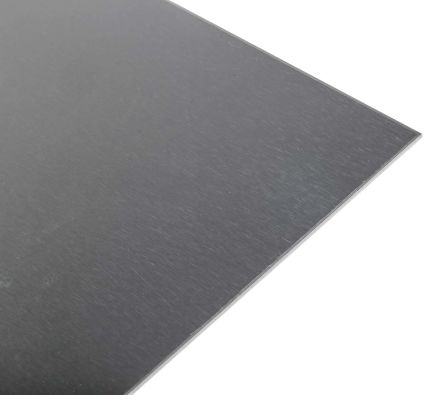
Aluminium sheets, also known as aluminium plates, are the result of basic raw-form aluminium being pressed and rolled into panel form under high pressure
Aluminium sheeting is characteristically manufactured to be very thin and lightweight, yet sturdy enough to offer extreme versatility alongside inherent ease of installation and maintenance. It also boasts numerous other unique and useful properties that make it very widely deployed today across an enormous variety of industrial, agricultural, home DIY and manufacturing/production applications.
A range of additional coatings applied to aluminium sheets can help create a long-lasting material for use in outdoor settings or other challenging environments, such as for exterior cladding. The extremely lightweight nature of very thin sheet aluminium makes it ideal for use in drinks cans, food containers and other everyday products suitable for high-volume storage, transport and retail.
Surface dimensions and thickness are the primary factors to consider when looking at options to buy aluminium sheeting in the UK. While overall surface area is the first key aspect you’ll want to consider in planning a job using this sort of sheet metal, the various material finishes available will also play a significant part in helping you select the ideal sort of aluminium sheet for your needs and intended applications.
Anodised aluminium sheeting, for example, can provide both robust protection against corrosion and a more aesthetically pleasing outer face, while raw or unfinished sheets can be coated or protected in a variety of other ways once initial forming and fabrication is complete. Suitable for use with rivet and plate fixings as well as for welding purposes, aluminium plate is viewed as an especially user-friendly sheet metal, featuring high formability and being easy to cut to size for a diverse range of applications.
It’s commonly cut to 1mm-2mm thick, and at this weight it can be formed easily by hand or with smaller handheld tools. Thicker plates may require either manually operated forming machines, or more industrial-type pneumatic presses or brakes to work into the desired shape.
Types of aluminium sheets
There are numerous types of aluminium sheets available to buy on today’s market. In this section, we’ll look briefly at some of the more common aluminium sheet products you’ll find for sale from various suppliers and manufacturers.![]() |
Perforated aluminium sheetsA perforated sheet or plate aluminium is also used in scenarios where it’s chosen chiefly for its aesthetic qualities - this is particularly common in interior/exterior design work, for example in constructing many kinds of floors, ceilings, screens, sun shades and other architectural or decorative panels. Other typical applications might include the food industry, factory or laboratory environments, where it’s widely found performing sluicing, drainage and collection roles in industrial washing and drying stations. |
![]() |
Chequered aluminium sheetsAluminium chequered plates are panels of sheet metal that have raised hatch marks on one side (the reverse side is untextured), forming a raised pattern that’s usually embossed to a height of around 1.5mm. Known variously as checker plates, tread plates, 5 bar sheets or durbar floor plates, they’re most often made from aluminium, although steel versions are also sold. |
![]() |
Anodised aluminium sheetsAnodising is an electrochemical process used to increase the thickness of the oxide layer on a metal’s surface. Aluminium anodised sheets not only increase resistance to corrosion and wear (once a sealant has been applied to combat the porous qualities of heavily anodised metal), but it can also prime the plates for better adhesion of paint, dyes, films, glues and other cosmetic flourishes than bare metal offers. As a result, anodised metals are commonly represented by highly coloured aluminium sheets or other decorative panels, such as those widely used in vehicle parts, smartphones, tools, cookware, sporting goods and architectural materials. |
![]() |
Composite aluminium sheetsAluminium composite sheets or panels, frequently abbreviated to ACS or ACP, are manufactured from two very thin pieces of coil-coated aluminium bonded to the outside of a non-aluminium core (often plastic). They’re commonly used as lightweight but robust panels for external cladding or building facades, as well as in a wide range of insulation and folding panel applications. Aluminium composite panel sheets, sometimes called sandwich panels or dibond sheets, are much lighter than solid metal equivalents. This makes them far easier to install and maintain in day-to-day use, and they’re generally much easier to machine, cut and shape neatly using simple tools. As such, they’re an excellent choice for weatherproof signage and sign trays (especially where more intricate design work such as decorative lettering is required), as well as for fascia panels, column cladding and other exterior decorative elements. |
![]() |
Brushed aluminium sheetsMany different types of aluminium sheeting are available in either brushed or unbrushed variants, including anodised and composite panels. ‘Brushed’ in this context refers to a fairly uniform pattern of light parallel scratches and scuffs, deliberately introduced across the surface of a metal sheet to impart a satin-like finish. The effect is widely seen on all manner of internal fixtures and fittings. Opting to buy brushed aluminium sheet is often a primarily aesthetic decision - the brushed look is hugely popular worldwide as a stylistic flourish that dulls the reflective qualities of otherwise polished surfaces. Although brushing is, in fact, the result of additional secondary processing that results in a satin finish, as a design element it can (somewhat counterintuitively!) help to give a raw or unprocessed ‘industrial’ look. It’s often used to highlighting the fact that certain objects or panels are made from metal, in contrast with areas made from other materials. |
Properties of aluminium sheet metal
Aluminium sheets are arguably among the most widely used types of abrasives and engineering materials today. This is largely due to some key aluminium sheet metal properties which, when viewed in combination, set it apart from other metal plate types for ideal use in a broad array of environments and applications.
Its most valuable properties include:
- Lightweight (around 1/3 the mass of steel by volume), so an extremely cost-effective solution in transport and logistics-based operations
- Strong enough to be suitable for various building and structural applications
- Resistant to corrosion in outdoor and moisture-exposed applications
- Easily formable, with a relatively low melting point (660 celsius) even at thicker gauges
- Suitable for food-grade uses, including direct contact packaging, due to being non-reactive and completely impermeable to smells and flavours (even at extremely lightweight foil thicknesses)
- Fireproof - will not burn except in very thin films, and releases no toxic gases when melted
- Highly reflective, making it suitable for use in energy-efficient heating and lighting systems
- Excellent conductive properties for both heat and electricity (roughly twice that of copper), again making it suitable for economical heat and power systems
- Easily recyclable, with low loss rates during breakdown (around three-quarters of all the sheet aluminium ever made is still in active circulation today)
- Long-lasting and low maintenance, for reduced replacement rates and lower environmental impact
- Available in a practically unlimited range of thicknesses and sheet sizes
How are aluminium sheets made?
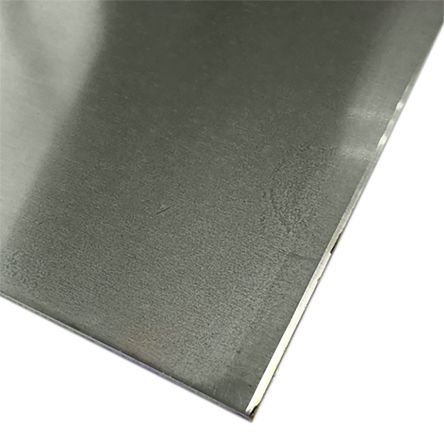
Aluminium is currently extracted exclusively from raw bauxite, an ore found in heavy clay-like soil types several metres below the surface of the ground. This ore is then refined in a hot lime and caustic soda solution, producing alumina, a white oxide powder. When combined with electricity and carbon (to create CO2) at high temperatures, this oxide produces the liquid metal we call aluminium.
This liquid metal is then formed into different sorts of ingots or alloys, depending on what its eventual application will be. Aluminium intended for tubes, rods, sheets and angles is usually formed into ingots which can measure up to 20 feet in length (and weigh up to 20 tons!), but which have extremely formable (ductile) properties. This makes it easy to roll or press them under varying temperatures and pressures to produce plates, sheets, foils and other forms of almost any useful thickness.
What are aluminium sheets used for?
Given their numerous unique and handy properties, aluminium sheet uses are almost too varied and widespread to provide an especially comprehensive list. However, in this section we’ll touch on some of the more common applications of aluminium panels and plates, found throughout a wide range of everyday industry, design and construction environments.
-
- Roofing - aluminium roofing sheets are among the most frequent applications of larger panels, due to their lightweight but sturdy construction with excellent anti-corrosion properties.
- Artistic ceilings - dibond or composite aluminium sheets are very often used as interior ceiling panels or large tiles, offering a highly decorative but hard-wearing design feature.
- Balconies - aluminium balcony railings and balustrades are common, once again thanks to their lightweight but rigid construction and the fact that they’re highly weatherproof.
- Drinks cans, beer barrels and other food industry containers - as well as all manner of sealed food storage solutions, you’ll often see reusable aluminium beer kegs for sale from wholesalers and suppliers, where the material is equally prized for its non-reactive, non-tainting and impermeable qualities, as well as being lightweight for economical shipping.
- Cable sheathings - metal sheathing for cable is commonly formed from aluminium foils and other extremely thin aluminium sheets, due to the fact that it’s relatively corrosion resistant (and is easy to make more so with various additional treatments), as well as showing impressive mechanical and electrical characteristics.
- Cladding and fascia panels - aluminium composite sheeting is always a leading choice for exterior cladding, internal insulation and other design-led panel applications in a wide variety of industrial, commercial or domestic buildings and installations, thanks to being resistant to the elements, lightweight, sturdy, and easily coloured or decorated
- Cranes, trusses, supports and lifting gear - lightweight materials used in the lifting industry (for example on extension forks, lifting booms, load plates, pipe cradles and support trusses) can help boost productivity and reduce energy costs, as well as making bulky items of lifting equipment and machinery far more portable for jobs in confined or difficult-to-access spaces.
- High stress applications - 6082 aluminium is a medium strength structural alloy with excellent corrosion resistance, making it ideal in a range of more force-intensive applications such as T6 aerospace grade aluminium and alloys for automotive structures.
- Lamp reflectors - the superb reflective properties of aluminium sheet, in terms of both heat and light, make it an ideal product for use in a wide range of commercial or domestic aluminium reflector lamps and heat forwarding lamps.
- Shelters - aluminium panels are widely used in the UK and elsewhere to construct lightweight yet durable covered shelters and outdoor walkways in public areas, workplaces and private homes.
- Caravans - towable storage and accommodation is often constructed largely from aluminium plate or sheeting, making it lighter to haul and offering great resistance to weathering in exposed areas.
- Flooring and walls - aluminium plate can be chequered to provide improved anti-slip and damage-masking properties, ideal for use in high traffic areas, while both decorative and structural aluminium sheet walls have become increasingly popular as hard-wearing, attractive and easily cleaned fixtures in the home or workplace.
What sizes do aluminium sheets come in?
There are a wide variety of aluminium sheet, plate and foil sizes sold around the world. Generally speaking, any aluminium panel between about 0.2mm to 6.5mm thick is usually considered an aluminium sheet, whereas thinner gauge products than this would typically be classified and sold as foils. Thicker gauges than 6.5mm (roughly a quarter of an inch) are most often referred to as aluminium plate.
The right choice for a given application will depend entirely on the degree of flexibility/rigidity required for the sheet to perform its intended function.
Thickness (mm) | Gauge number | Common uses |
---|---|---|
1mm | 19 | Often used for light cladding or panelling, particularly when used in the construction of aluminium composite or sandwich board. |
3mm | 11 | 3mm aluminium sheet is often found on slightly thicker panels, such as interior wall coverings or perforated privacy screens. |
5mm | 6 | 5mm aluminium sheet is at the upper end, thickness-wise, of what would still generally be referred to as a ‘sheet’, rather than a ‘plate’. |
6mm | 4 | Often selected for walkways and floor coverings intended for use in high traffic areas, particularly when sold as chequered or durbar plates. |
10mm | 0000 | Thicknesses of 10mm and above is often manufactured to 6082 alloy specifications, making it suitable for more robust applications such as in heavy duty or military environments, panels for heavy machinery and large-scale transport, skips, construction and industrial waste management, or larger sterile/food-grade containers for the agricultural and production sectors. |