- Published 11 Mar 2024
- Last Modified 11 Mar 2024
- 12 min
Electronics Testing Guide

We all own some form of electronics as they play a huge role in modern society, from information processing, telecommunication, and signal processing to the development and distribution of the very device you’re reading this guide on.
Electronic devices and the components that they are comprised of have a profound effect on our lives, which is why electronics must pass stringent tests when they are produced and brought to market for functional, legal and safety purposes. This is also true for the lifecycle of an electronic product as they can gradually degrade over time, leading to failures, lower performance, and safety issues.
Where to Start with Electronics Testing?
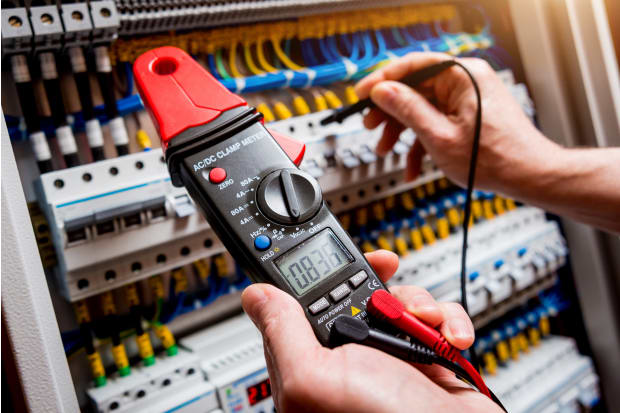
There is a multitude of testing equipment when it comes to electronic devices and equipment, all of which are designed to ensure optimum operation and safety in any environment, from domestic dwellings to industrial warehouses.
This guide will not only tell you why electronics testing needs to be conducted but will also help you develop knowledge in the following areas:
- Phases of electronics testing
- Equipment needed for electronics testing
- Different types of electronic tests
- Strategies for testing electronics
What is Electronic Testing Equipment Used for?
The most common applications of electronic testing equipment include:
- Testing performance of the circuit and possible defects during the research & development (R&D) phase
- Identification of component level defects, faulty circuits, overloading connections, and high resistances during production testing
- Checking the overall performance of the electronic device and verifying it against the design specifications
- Verification of basic electronic parameters such as voltage, current, resistance, conductance, and capacitance. This could be applicable both in the design phase and regular maintenance of the device (if a measurement instrument)
The testing of electronics is segmented into phases before distribution and usage. This is done to troubleshoot any potential problems and eliminate them, so the product can operate at an optimum level.
If you design or manufacture any type of electronics equipment, the appropriate electronics testing procedures must be completed at the different stages of the product lifecycle, including:
- R&D testing of a proof of concept
- Design - testing a finalised design against specification
- Manufacturing or production test of each unit produced or samples thereof
- Installation and commissioning testing for specialised equipment
- Periodic calibration - if measurement instrumentation
- Troubleshooting - when equipment fails
- Periodic safety testing of hardware
Certification Testing
Once the respective stages have been completed successfully, the DUT (Device Under Test) will be suitable for use. However, it is also important to note that electronic devices must continue to be maintained under manufacturer specifications, per legislation, and in correspondence with regulatory guidelines.
Equipment Needed for Electronics Testing
So now you know why and when you need to test electronic equipment, it is important to know how to test electronic equipment and the various types of equipment used in electronics testing. This guide will cover the essential testing equipment required for different stages in the product lifecycle, from small-scale component testing to large-scale production testing.
Components Testing
The testing of electronic components is undeniably important, ensuring the circuit is built as safely as possible before being installed in a product. Considering the millions of electronic components produced each year, manufacturers can’t comprehensively test every single component off the production line. Statistical process control and random sampling ensure their components are manufactured to their required specifications, focussing on four areas:
- Components that will fail early in their product life before they are added to a PCB assembly (PCBA) are identified through Highly Accelerated Life Testing (HALT) and Stress Screening (HASS). This can include vibration and shock testing, electrical stress testing, and burn-in testing
- Electrical testing verifies the components meet the rated electrical specifications as well as ensuring a PCBA meets basic electrical requirements. Automated testing equipment can check for electrical connectivity in the bare PCB and finished PCBA at a minimum. The designer needs to specify test data to the manufacturer for this stage to be carried out
- PCBAs and batches of components are put through reliability testing that tests their ability to withstand extreme mechanical loads or environments
- Functional testing is normally carried out by test engineers once a prototype is fabricated, at which point the system is tested against the predetermined performance requirements. In this case, the individual components are only tested if the board fails, and the root cause needs to be narrowed down to a specific component
Common Components Testing Equipment
Common component testing equipment includes:
- Component and IC testers – Integrated Circuit (IC) testers are battery-powered portable devices ideal for testing components such as batteries, diodes, LEDs, SCRs, and transistors. They can measure parameters such as voltage, resistance, capacitance, continuity and more
- Decade Boxes – used to substitute standard value components in a circuit, decade boxes consist of a series of resistors, capacitors, and inductors to replicate different electrical values. They allow the accuracy of test equipment to be verified before use, as well as being used for troubleshooting purposes
- Ohmmeters – Ohmmeters are used to measure the electrical resistance and continuity of an electrical circuit and its components. By passing a small current through the sample, the instrument can measure the resistance by the voltage drop that is produced when the current passes through said sample
Electronics Test Equipment
The comprehensive testing of an electronics circuit requires a variable number of different test equipment devices depending on the nature of the application. This is to ensure the DUT is adequately powered, fed with representative signals, and that outputs are assessed against the specification. This is also to enable the test engineer to gain an understanding of how the whole circuit is behaving by being able to monitor (and potentially decode signals within) any part of the circuit.
These devices can often be remote controlled and operated by test scripts to facilitate high-speed production testing.
Common test equipment for use throughout the various stages of a design’s life includes:
Bench Power Supplies
To generate accurate and fully controllable DC supply at the required voltage and current.
Oscilloscopes
Capture, process, display and analyse detailed information about electronic signal waveforms.
Function Generators
Produce waveforms including sine, square, triangular and sawtooth to feed into the DUT.
Signal Generators
Designed to provide highly accurate and stable signals at a given frequency and amplitude, with or without modulation applied.
Spectrum Analysers
Enable the analysis of the output of the DUT across the frequency spectrum.
Multimeters
Whether high accuracy bench digital multimeters (DMMs) or hand-held, these are effective for specific measurements of voltage, current, resistance, even sometimes capacitance and frequency. Bench DMMs can also support high numbers of measurements per second, perfect for production test situations.
Electronic Loads
Simulates an electrical load to test the power output of a DUT, whether that be for RF or high-power applications such as motors.
Logic Analysers
Allow investigation into digital signals, including timing issues, protocol decoding and related problems. This capability is now frequently available on Mixed Signal Oscilloscopes (MSO).
Data Acquisition
Monitor the DUT for extended periods, and capture key variables such as voltage, current, temperature, pressure or sound for detailed analysis.
EMC Testing
Electromagnetic Compatibility tests (EMCs) ensure that the equipment or systems can function satisfactorily in their environments without causing intolerable electromagnetic disturbances to anything else in the area. These tests also ensure that the equipment will not be adversely affected by interference from other devices or naturally occurring sources of interference (immunity testing).
EMCs are mandatory in most markets, including Europe and the United Kingdom, the United States, China, Korea, Australia, and New Zealand.
Depending on the product or device under test, there are different tests required to achieve EMC certification – called a Declaration of Conformity – including but not limited to:
- Antenna input immunity
- Antenna screening effectiveness
- Conducted disturbances immunity
- Conducted emissions (continuous and discontinuous interference)
- Electrostatic discharge (ESD) immunity
- Electrical fast transient/burst immunity
- Harmonic current emission
- Immunity from radiated fields
- Immunity to induced voltages
- On-site EMC testing
- Power interference
- Power supply conditioning
- Radiated emissions
- Radiated field immunity
- Voltage fluctuation/flicker
- Voltage surge immunity
- Voltage dips/interruptions immunity
- Magnetic field measurement (EMF)
- Electric field measurement (EMF)
- Electromagnetic field measurement (EMF)
- Induced current density due to the electric field (EMF for lightning equipment)
ESD Testing
Electrostatic Discharge (ESD) testing falls under the EMC umbrella but is perhaps one of the most well-known EMC tests and is used across a multitude of industries. ESD can occur between two electrically charged objects wherein electricity is suddenly transferred between them, an event that can be caused by direct contact, an electrical short, or a dielectric breakdown. While this discharge or visual spark is not lethal on its own, it can render devices and equipment dysfunctional, leading to replacements or repairs.
ESD events can be extremely harmful when they occur in the presence of electronics as they can cause immediate failure or slowly damage the components over time. While this is a gradual process, the latent damage will eventually lead to the component failing, causing costly replacements that can also cause downtime in the wider system.
By simulating various electrostatic impacts that may occur during transit or operation, ESD testing determines whether a product complies with the requirements of its ESD protective area and procedures. These tests can be carried out in one of two ways - either the air method or the contact method:
- The air method involves positioning a charged generator or discharge object (an ESD gun, for example) towards the device under test. Variables such as humidity and temperature can impact ESD testing, with ESD events more commonly occurring in low temperature and low humidity environments
- Contact testing eliminates the environmental variables that can affect the air method. Using this method, the ESD generator is in direct contact with the device under test and is kept in contact throughout the entire duration of the test. While this test method is typically consistent across different environmental conditions, contact ESD rarely occurs naturally and therefore the results may be considered unrealistic
Portable Appliance Testing
While tests of an electronic circuit are primarily focused on operation to specification, ensuring the complete product (including mains voltage electrical circuits) is safe for users is another key consideration.
The design must meet the relevant electrical standards for the country the product is to be supplied to and should be tested to these regulations before shipping using appropriate test equipment. This includes earth bond testers, insulation testers, and similar.
When the equipment is in use, organisations and individuals, such as employers and landlords, are legally required to create a safe working environment and PAT testing is a great way to mitigate risk.
PAT Testing
Portable Appliance Testing, or PAT Testing for short, is used to check how safe electrical appliances are for use through visual and electronic tests.
A competent person with suitable knowledge of electronics must carry out PAT Testing to be compliant with legislation such as:
- Health and Safety at Work Act 1974
- Electricity at Work Regulations 1989
- Provision and Use of Work Equipment regulations 1998
- Management of Health and Safety at Work regulations 1999
You will need to use the correct PAT testing equipment appropriate for the products under test. After the appropriate person has completed the testing and the products have passed, they will issue a PAT certificate signifying that the appropriate standards have been met and the product is safe for use.
What Do You Need to PAT Test?
There are 7 categories of appliances that require PAT testing:
- Fixed appliances
- Stationary appliances
- IT appliances
- Moveable appliances
- Portable appliances
- Cables and chargers
- Handheld appliances
Electrical appliances are mainly categorised as Class 1, 2 or 3, with Class 1 being the most dangerous if unsafe and Class 3 the least dangerous if unsafe. The class of an appliance helps determine the level of PAT testing required for the equipment so it can be used safely. Class 1 appliances need a full PAT test, Class 2 appliances need a PAT insulation test, and Class 3 appliances don’t need to be PAT tested at all.
Class 1 appliances are typically made of metal, have three cables, a metal Earth pin, and a fuse in the plug. They include small and large white goods, such as microwaves, kettles, toasters, refrigerators, and microwaves.
Class 2 appliances include additional insulation and therefore do not rely on a metal Earth pin for protection, with items such as hairdryers, televisions, computers, and photocopiers falling under this category. However, the safest way to ensure the class of your products is to look for the Class 2 appliance symbol.
Finally, Class 3 items are low voltage appliances and are considered the safest of electrical appliances, such as laptop computers, mobile phones, and low energy lightbulbs. While the items themselves may not require PAT testing, their charging leads and plugs may require testing.
Calibration of Electronic Measurement Devices
Electrical calibration is a means of verifying or adjusting the performance of any instrument that measures or tests electrical parameters such as voltage, current, resistance, inductance, capacitance, time, and frequency.
Using precise devices that evaluate the performance of these key properties, electrical calibration can allow users to carry out performance evaluations and calibration adjustments where required, allowing for potential errors to be identified or minimised. There are two broad categories for these precision devices - calibrators/standards, and precision digital multimeters.
- Calibrators – calibrators are usually able to provide a wide range of precision output signals, such as voltage settings ranging from as little as a few microvolts to a maximum of about one kilovolt on most models. Modern calibrators commonly provide outputs for various electrical functions, including voltage, resistance, and current
- Standards – considered to be even more precise than calibrators, standards are capable of performances at least four times better than calibrators, though this is usually limited to one electrical function with one or few output settings in comparison
- Precision digital multimeters (DMMs) - DMMs provide excellent measurement performance of various electrical parameters including voltage, current, and resistance through several values. Frequency, capacitance, and other parameters can be included but are less commonly found on DMMs
Popular Electrical Testing Equipment
Check out our range of electrical test and measurement products below:
Related links
- A Complete Guide to Magnetic Tape
- A Complete Guide to PID Temperature Controllers
- Choosing the Right Digital Multimeter for Your Electrical Testing Needs
- A Complete 3D Printer Buying Guide
- A Complete Guide to Cable Ties
- The Complete Guide to Cordless Drills
- Push Button Switches: A Complete Overview
- Everything You Need to Know About HDMI Connectors