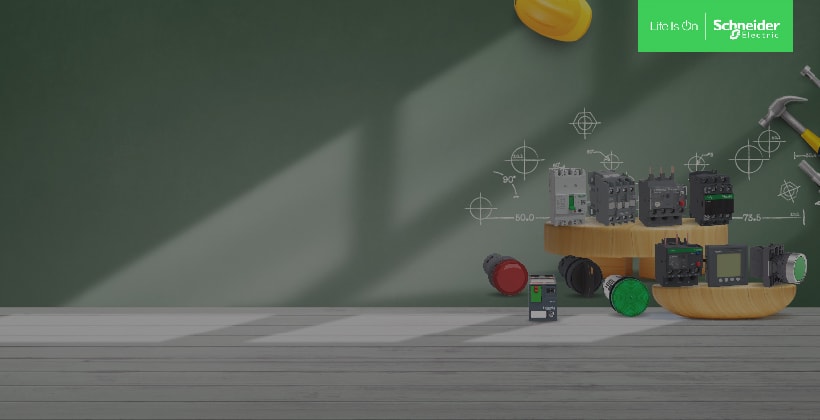
Buy More, Get More with Schneider!
Why not stock up and enjoy the benefits? Let’s make your next project even more rewarding!
Enjoy up to 20% off selected products in Facilities & Maintenance and Electrical categories.
Maximize Your Performance with Fluke – Now at a Special Year-End Discount!
Be part of our campaign today and stand a chance to win RM150 Touch & Go Voucher and more!
Explore our wide selection of Development Kits from top brands.
Helps reduce your supplier base while cutting purchase-to-pay costs and freeing up valuable time.
Click here for new products this month. A wide range of industrial equipment one after another.